Key Strategies for Enhancing Business Processes
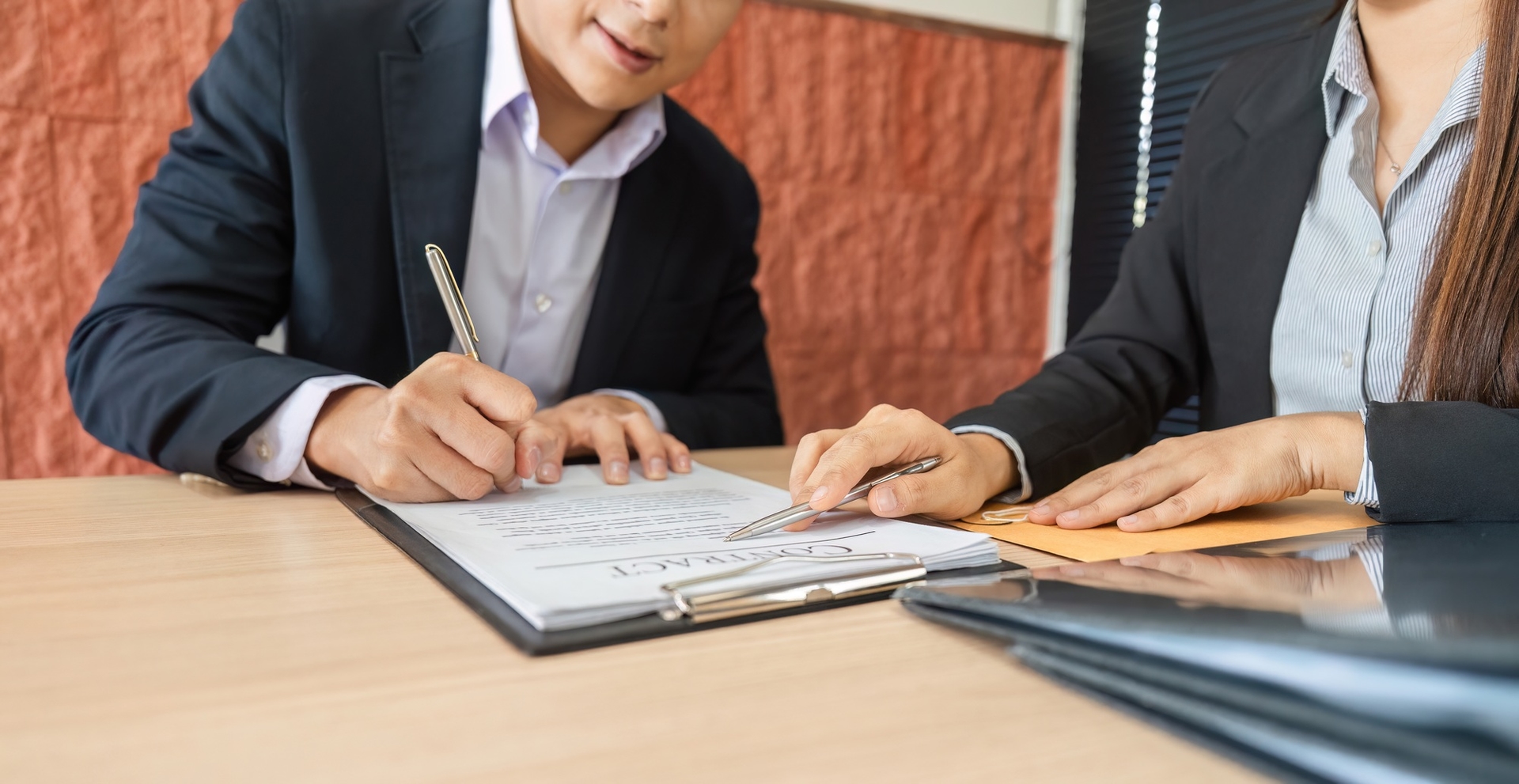
Enhancing business processes is critical for improving efficiency and achieving organizational goals. By adopting methodologies like Six Sigma and Lean, you can identify inefficiencies and eliminate waste. Engaging stakeholders throughout the process encourages collaboration, whereas visual mapping techniques help pinpoint bottlenecks. Establishing clear, measurable objectives is fundamental for focused improvements. As you explore these strategies, you’ll find that continuous monitoring and iterative adjustments play an important role in maximizing operational effectiveness. What are the next steps to implement these changes?
Key Takeaways- Identify and prioritize time-consuming processes to target for improvement, ensuring focused efforts yield significant results.
- Set clear, measurable goals for each project to guide progress and assess impact effectively.
- Utilize visual mapping techniques to uncover inefficiencies and streamline workflows for enhanced clarity.
- Engage stakeholders throughout the process to gather insights and foster collaboration, minimizing resistance to change.
- Implement a continuous monitoring system to evaluate the success of improvements and adjust strategies as needed.
Continuous improvement in business processes is vital for organizations that want to thrive in today’s dynamic market environment. By regularly evaluating and optimizing processes, you can identify and eliminate bottlenecks, leading to increased operational efficiency and reduced costs.
Utilizing continuous improvement methodologies like Six Sigma or Lean thinking provides structured frameworks to enhance your processes through waste reduction and quality improvement. Engaging stakeholders in this process promotes innovation and guarantees alignment with organizational goals.
Employing process improvement tools and following process improvement best practices can greatly boost your performance. In the end, adopting effective business improvement strategies and operational process improvement techniques empowers you to adapt to changing market conditions and meet customer expectations, ensuring your organization remains competitive.
Definition and Benefits of Business Process Improvement and OptimizationBusiness Process Improvement (BPI) and optimization focus on enhancing the efficiency and adaptability of an organization’s operations.
The process improvement definition involves systematically analyzing and redesigning workflows to achieve better quality, reduced costs, and increased customer satisfaction.
The benefits of process improvement are significant; they include fewer errors and faster completion times.
Continuous improvement tools and methodologies, like Six Sigma and Lean, provide practical frameworks for operational business process improvement.
Examples of business process improvement methods range from simple adjustments to extensive process improvement plans.
These strategies align with process improvement goals, such as enhancing manufacturing process improvement and ensuring compliance.
In the end, effective BPI encourages innovation and responsiveness to market demands, creating a more agile organization.
Steps to Improve and Optimize a Business ProcessImproving and optimizing a business process requires a structured approach that effectively identifies areas for improvement. Start by pinpointing a single process that’s time-consuming and resource-intensive; this focus maximizes impact.
Set clear business goals for your process improvement project, ensuring they’re measurable to track progress. Utilize process improvement methods and tools, such as creating a visual map of the existing workflow to identify inefficiencies.
Engage stakeholders throughout this process to gather insights that reflect their needs, enhancing business processes. Establish a goal-centric vision that aligns with your continuous improvement model, allowing for adjustments and ongoing evaluation.
Methodologies for Business Process ImprovementEffective methodologies for business process improvement are vital for organizations aiming to improve efficiency and quality.
Utilizing continuous process improvement tools like Six Sigma can systematically reduce defects through the DMAIC framework, augmenting overall performance. Lean methodology focuses on eliminating waste, streamlining processes, and increasing customer satisfaction.
Total Quality Management (TQM) cultivates a culture of continuous improvement, engaging all employees to elevate product quality. Value Stream Mapping (VSM) visually captures process flows, helping you identify inefficiencies and reduce lead times.
Furthermore, Kaizen encourages incremental improvements, promoting a proactive problem-solving culture. By applying these continuous improvement methods techniques, you can implement effective process improvement process steps that lead to significant gains in process and performance improvement.
Implementation and Continuous Improvement of the New ProcessSuccessfully implementing a new process requires careful planning and execution to guarantee that the intended improvements are realized. Start by analyzing the current process through mapping, which helps identify inefficiencies and bottlenecks.
Engage stakeholders during the redesign phase to encourage collaboration and minimize resistance. Utilize process improvement tools and techniques, applying a continuous improvement model to refine your approach.
Testing the new process on a smaller scale is essential; it allows you to spot unforeseen issues before full deployment. After implementation, continuous monitoring of the new process becomes crucial for adapting to market changes.
Establish clear, measurable goals to evaluate the success of your process improvements, ensuring alignment with overall business objectives and maximizing ROI through effective project management process improvement.
ConclusionIn summary, enhancing business processes requires a commitment to continuous improvement through structured methodologies like Six Sigma and Lean. By engaging stakeholders, employing visual mapping techniques, and setting clear objectives, you can effectively identify inefficiencies and drive focused improvements. Implementing these strategies not merely maximizes operational efficiency but likewise guarantees adaptability in a changing market. Regular monitoring and iterative adjustments further support this process, eventually leading to a more streamlined, effective organization that meets its goals.
Image Via Envato
Small BusinessTrends